After you first air seal your home.
Insulation is a key component of every Canadian home.
It acts as a thermal barrier to keep heat inside our homes in the winter and outside in the summer.
Even though the outside environment can vary dramatically, an energy efficient Canadian home can be comfortable year-round.
Insulating should be one of your first steps
Heating is the largest consumer of energy in your home. In order to reduce your heating bill, the first step is to improve your building envelope to reduce air leakage and reduce heat loss.
By choosing to do this first in any retrofit, you reduce the overall heating requirements of your home and can downsize your heating equipment saving upfront costs and long-term operating costs.
Ultimately, the more well-insulated and leak-free your building envelope is, the less energy you need to use to keep your home comfortable! By implementing whole-home building envelope improvement strategies, you can invest in a future-proof home today and reap the benefits of a healthier, comfortable, and quieter home.
Making insulation the first stage of your retrofit journey can help you reduce your monthly energy bills, make your indoor environment healthy and comfortable, and reduce the carbon impact your home has on the global environment.
“Our house is a lot warmer in the winter and there are fewer cold spots, especially near the outside walls…The upstairs is much more comfortable than it was before.”
Steve McMurtry – Homeowner in Peterborough
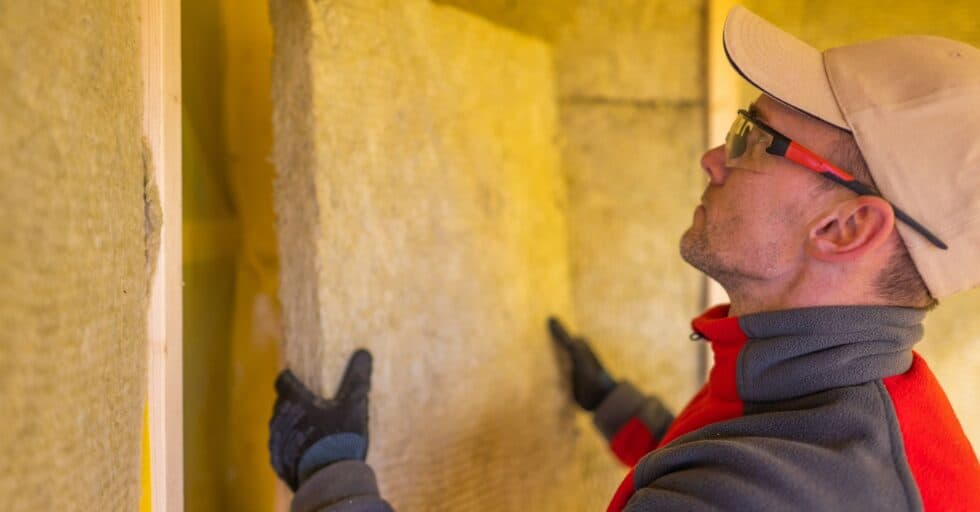
Types of Building Insulation
With so many different home insulation products on the market, it can sometimes be a difficult choice to make — and one that affects you, your home, and the environment. Luckily, your Registered Energy Advisor can provide you with advice and information on the different types and materials. We’ve listed some of the common types, below:
Batt insulation
- This common type looks like a memory-foam mattress topper, but fluffier and more fibrous.
Loose-fill insulation
- This type is great for hard-to-reach places as it can be blown in through relatively small gaps.
Spray-foam insulation
- Formaldehyde-based foamed-in-place urea insulation has been banned in Canada since 1980.
- This type of insulation is typically considered an environmentally unfriendly choice.
Rigid-board insulation
- A bit on the pricier side, but this one is more compact and typically used on the exterior or in tight spaces.
Common insulation materials include:
Cellulose fibre
- Removes carbon from the atmosphere when grown, and locks that carbon into your walls.
- Similar materials — like cork, hemp, or straw — are largely climate positive.
Mineral wool
- Produced using molten rock or slag by-produced in steel mills (e.g., Rockwool).
- Should be carefully handled as fibres can irritate airways, eyes, and skin.
Fibreglass
- Made by spinning molten glass into super fine fibres.
- A varying percentage of the raw glass used is recycled glass.
- Like mineral wool, fibreglass should be carefully handled as they can cause irritation to airways, eyes, and skin.
Polystyrene
- A petroleum-based product used in rigid-board insulation.
- Comes in expanded (EPS), graphite (GPS), and extruded (XPS) versions.
Polyurethane
- A sprayed foam product made from petroleum.
- Typically used to insulate older basements.
Polyisocyanurate
- Sometimes comes with aluminum-foil surfacing to further improve thermal performance.
- Ironically, this rigid-board material does not perform as well in colder climates.
Some other less common insulation materials are animal wool (typically sheep), recycled cotton and denim fibre, Icynene, and aerogel among many others.
Choosing the type and material of insulation for your home is best done in consultation with a Registered Energy Advisor. Installation of any insulation should be done by a qualified professional, as improper installation can lead to poor performance and increased costs.
Things to consider when selecting home insulation products
A lots of factors will influence the insulation products you choose for your home, including your budget, the available space you have, the structure of your building, the existing insulation (if any), and the climate you live in.
But, there are some other factors you should consider, too:
- The R-value of the insulation will tell you how effective it is, when installed properly.
- The materials used in the production of the insulation will inform you if the product could have negative impacts on your health or indoor air quality.
- The embodied or material carbon rating will tell you whether the production of that product had a negative, neutral, or positive impact on our climate. This last consideration is one that’s gaining attention. This is because, particularly for insulation, production-related carbon emissions (embodied emissions) can sometimes outweigh the climate benefits of using the material to reduce heat loss over time (operational emissions). But, embodied and operational emissions don’t have to be at odds! Organizations including Builders for Climate Action have developed tools (like the BEAM tool) to help you find the carbon footprint of your building materials and make climate-smart choices.
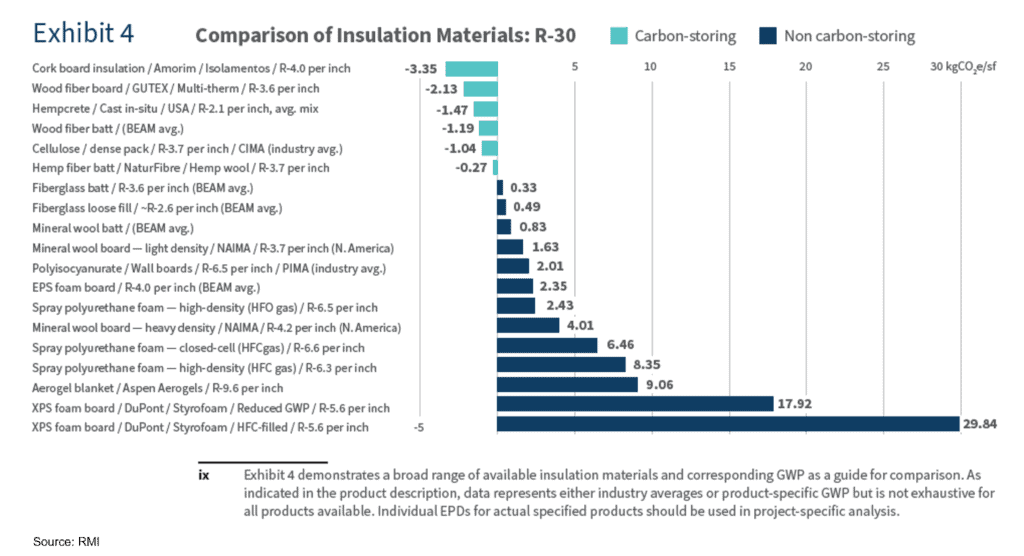
A Registered Energy Advisor can help you determine the best combination of energy solutions for your unique home and situation (budget, envelope construction, climate zone, etc.). Proper design of the thermal barrier and installation of insulation is the key to a healthier, comfortable, and more affordable home.
To learn more about the building envelope and how to make your old home run like new, read NRCan’s publication Keeping the Heat In.

Start your deep energy retrofit today.
Save energy. Make your home more comfortable.
Have less maintenance. Keep more money in your pocket.
Glossary
Insulation Values:
- Nominal RSI-value (R-value) of insulation (pre-construction) represents the resistance to the flow of heat of a given thickness of insulation. The higher the RSI-value (R-value), the better the insulation. RSI is the metric unit and is measured in m2°C/W while R is its imperial equivalent and is measured in ft2°F/W. RSI-1 = R-5.678.
- Effective RSI-value (R-value) of assembly (post-construction) represents the resistance to the flow of heat of the entire wall, ceiling or floor assembly considering the structure, insulation, framing, sheathing and all finishing. Typically this value is lower than the nominal RSI-value (R-value) of the insulation because the framing material has a lower RSI-value (R-value) than the insulation.
For example, wall studs and top and bottom plates will reduce the effective insulation value of an insulated wall; while sheathing, drywall and the exterior finish can increase a wall’s thermal resistance. In practical terms, for example, RSI 3.52 (R-20) batt insulation in a 2 x 6 wall might yield an effective insulation value of only 2.99 (R-17).
Loose-Fill Insulation: Loose-fill insulation options include cellulose fibre, glass fibre and mineral fibre. Loose-fill insulation is suitable for walls and floors and excellent in attics and enclosed spaces, such as roofs, where the space between the joists may be irregular or cluttered with obstacles.
Read more about loose-fill insulation and other insulation types in Keeping The Heat In – Chapter 3: Materials: 3.1.5 Summary of insulation types – Batt or blanket insulation
Low-E Coatings: Low-E, or low-Emissivity, glass has a fine coating of metal to reduce heat loss in the winter and heat gain in the summer, through the glass, by up to 30 percent. There are two types of low-E coatings: hard coat and soft coat. Both increase energy efficiency; however, some types of soft-coat low-E glass can dramatically reduce the amount of the sun’s heat coming into the home.
U-Factor: A measure of the heat transferred (or lost) through windows and doors. The lower the U-factor, the better the energy efficiency of a window. The inverse of U-factor (1/U-factor) identifies the heat resistance, expressed in RSI. The higher the RSI, the better the window is at resisting heat loss. You can use these values to choose windows to capture the heat from the sun or to reduce heat loss.
Vapour Barrier: The vapour barrier resists the diffusion of water vapour from the inside to the outside of the building envelope. It protects the insulation and structure from moisture damage that can be caused if water vapour moves into and condenses in the envelope assembly. In some applications, the vapour barrier also acts as the air barrier by reducing heat loss as it prevents air from passing in and out through the envelope (i.e. an air and vapour barrier).
Read more about air and vapour barriers in Keeping The Heat In – Chapter 2: How your house works: 2.3.1 Air leakage control — weather barriers, air barriers and vapour barriers